Keeping Construction Projects on Track with Reliable Concrete Testing
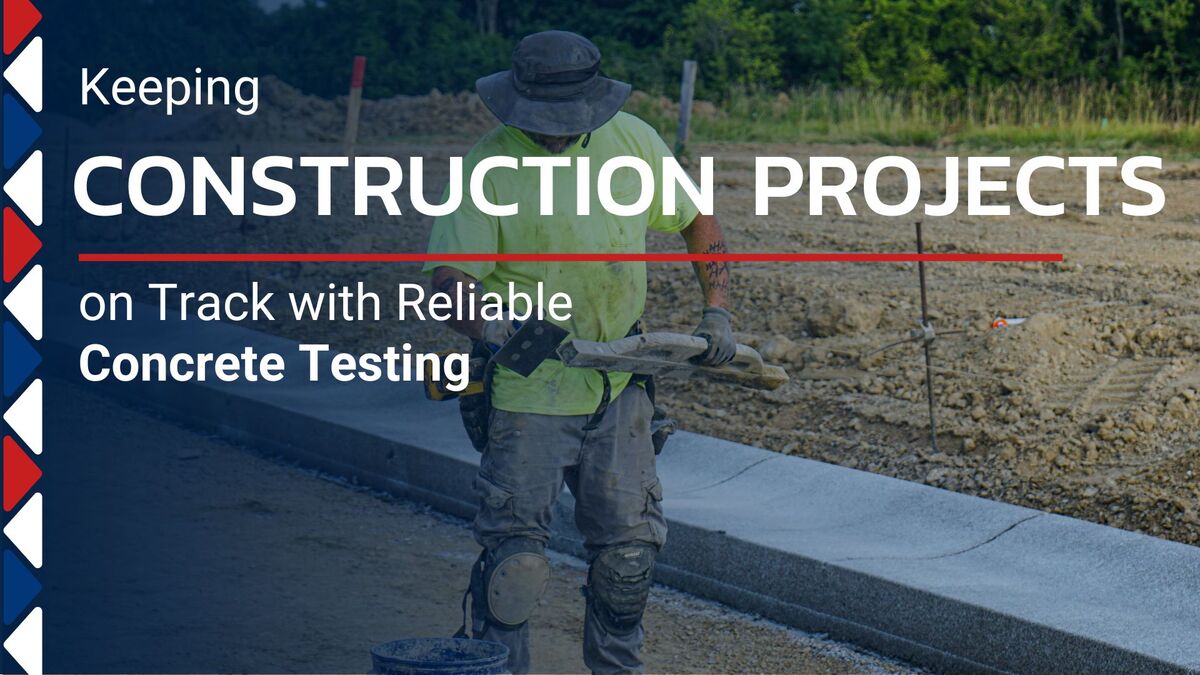
Construction projects depend heavily on concrete quality. It forms the foundation for structural integrity, project safety, and overall success. However, overlooking thorough concrete testing can create significant risks—structural failures, compliance issues, and costly repairs down the road. Concrete performance varies considerably due to factors like mixing, environment, and curing conditions. By following established industry standards like ASTM guidelines, we can avoid these pitfalls and deliver reliable, safe, and lasting structures. This blog will guide you step-by-step through the most impactful concrete tests, explaining their importance clearly and practically. Read on to get actionable insights you can apply to your projects today.
The Importance of On-Site Concrete Testing
Concrete quality directly impacts our construction outcomes, influencing strength, durability, and compliance with regulations. Since concrete doesn't always achieve full concrete strength exactly at the commonly presumed 28-day mark, consistent testing across various curing stages is necessary. When compressive strength of concrete isn't adequately assessed, structures become susceptible to unexpected failures, compromising safety and escalating project costs.
There's a common misconception in our industry—assuming that properly mixed concrete naturally achieves full strength. Reality tells a different story: variables like curing conditions, the water-cement ratio, and ambient temperatures significantly impact the final product. Regular on-site testing gives us control, enabling adjustments before issues escalate, and guarantees our final structures meet ASTM standards and project specifications.
Industry Standards and Guidelines for Concrete Testing
Our industry relies heavily on ASTM (American Society for Testing and Materials) standards. These guidelines establish uniform, precise testing methods, making sure we meet quality expectations and regulatory demands.
- ASTM C39 governs the process of evaluating concrete's compressive strength.
- ASTM C143 describes procedures for performing a slump test, measuring concrete workability.
- ASTM C31 focuses on the curing and field testing of concrete specimens.
Other relevant organizations, like the American Concrete Institute (ACI), supplement these standards, providing additional insights and testing methods. Following these standards not only supports compliance but also enhances safety, reliability, and consistency across projects.
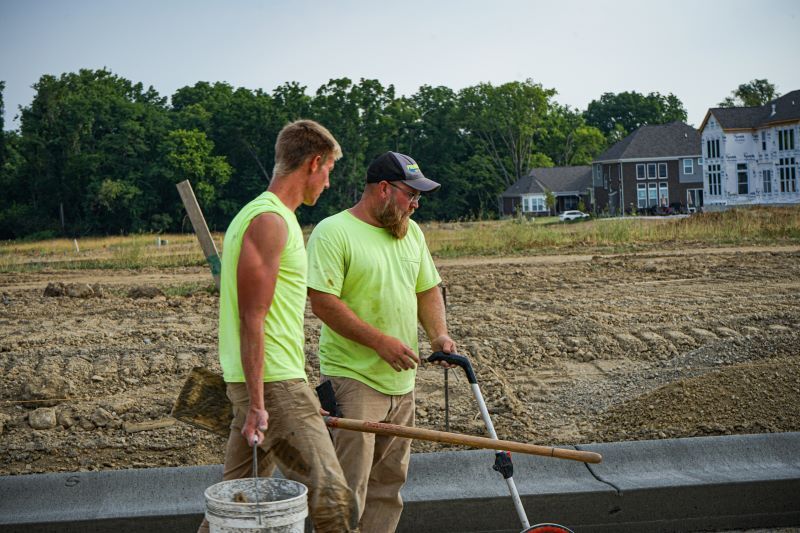
The Standard Concrete Tests and How to Perform Them
Reliable concrete evaluation combines several tests, each designed to measure specific qualities such as strength, workability, durability, and moisture content. Using a variety of testing methods allows us to pinpoint potential issues effectively and proactively manage concrete quality.
Slump Test: Measuring Concrete Workability
A slump test indicates concrete consistency and its ease of placement and finishing. If a concrete mix has excess water or too little moisture, its durability and strength will inevitably suffer.
Here's a step-by-step guide for conducting a slump test:
1. Fill a slump cone mold in layers, compacting each thoroughly.
2. Smooth the top, lift the cone steadily upward without twisting.
3. Measure the distance the concrete slumps or settles from the original height.
A typical standard slump for slab concrete is around four inches. When you encounter terms like an '80 slump,' it refers to 80 millimeters (approximately 3 inches). Excessively high or low slump values indicate improper concrete mix proportions or unsuitable water content.
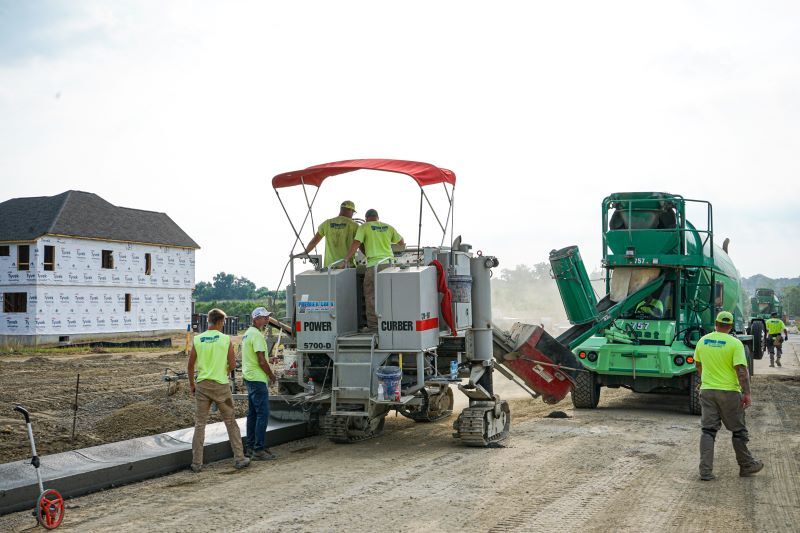
Compressive Strength Test: Ensuring Structural Integrity
Assessing the compressive strength of concrete is arguably the most important evaluation. The test involves creating cylindrical or cube concrete samples, which we test at specified intervals—typically at 7, 14, and 28 days—to monitor strength gain over time.
The 7-day cube test, specifically, acts as an early strength indicator. Although full strength often occurs around 28 days, these preliminary tests help predict final performance and alert us to potential issues early on. Mix design, curing conditions, and water-cement ratios all significantly impact the final concrete strength, making consistent, controlled testing indispensable.
Air Content Test: Controlling Durability in Harsh Conditions
Concrete exposed to freeze-thaw cycles or harsh conditions requires appropriate air-entrainment to remain durable. The concrete air test measures entrained air volume, significantly influencing concrete longevity.
Two standard ASTM-approved methods measure air content:
- Pressure Method (ASTM C231): Uses pressure changes within a sealed container to determine air content.
- Volumetric Method (ASTM C173): Suitable for concrete with lightweight aggregates, it measures displaced water volume.
Maintaining proper air levels safeguards against surface spalling, cracking, and long-term durability challenges, especially in cold climates.
Non-Destructive Testing Methods: Evaluating Concrete Strength Without Damage
Sometimes we must assess concrete strength without compromising existing structures. Non-Destructive Testing (NDT) methods make this possible, providing insights into concrete integrity safely and efficiently. Common NDT methods include rebound hammer testing, ultrasonic pulse velocity testing, and penetration resistance tests.
Though incredibly useful, NDT methods have limitations—they primarily provide relative indications of strength rather than absolute values. For comprehensive results, NDT should be complemented by periodic destructive tests like standard compressive strength evaluations.
Best Practices for Conducting Reliable Concrete Tests
Accurate results depend upon carefully handling concrete samples and strictly adhering to ASTM standards. Implementing these best practices ensures precision and consistency:
- Test concrete at specified intervals (7, 14, and 28 days).
- Properly cure samples under controlled conditions to reflect actual project scenarios.
- Prevent sample contamination by using clean equipment.
- Maintain precise water-cement ratios to achieve the designed strength and durability.
Avoid common mistakes, including inadequate compaction, poor curing conditions, or incorrect testing intervals. A commitment to best practices enhances your project outcomes, boosts your team's efficiency, and builds confidence in your structures.
Bring Confidence to Your Concrete Projects with Charles H. Hamilton
At Charles H. Hamilton, concrete isn't simply part of our job—it defines our expertise and reputation. Our team understands the importance of precise, reliable testing, and we adhere strictly to ASTM standards, reinforcing the durability, safety, and compliance of every structure we build.
We actively partner with our clients, providing expert concrete testing services and professional consultation to make sure your project stays on track and within specification. Whether you're concerned about the density of concrete, assessing moisture content through a concrete moisture test, or evaluating strength through compressive strength tests, our experienced team delivers trustworthy, actionable insights.
Contact us today to discuss your concrete testing needs, or learn more about our full range of services at Charles H. Hamilton’s Premier Curb of Cincinnati. Our commitment to your project's success makes us a dependable partner, ready to support every concrete challenge you encounter.